Dual color sole machine
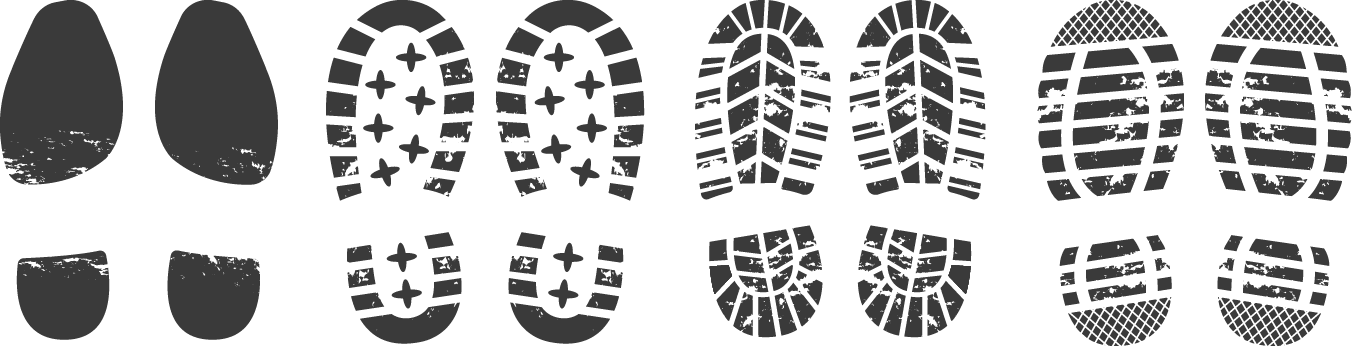
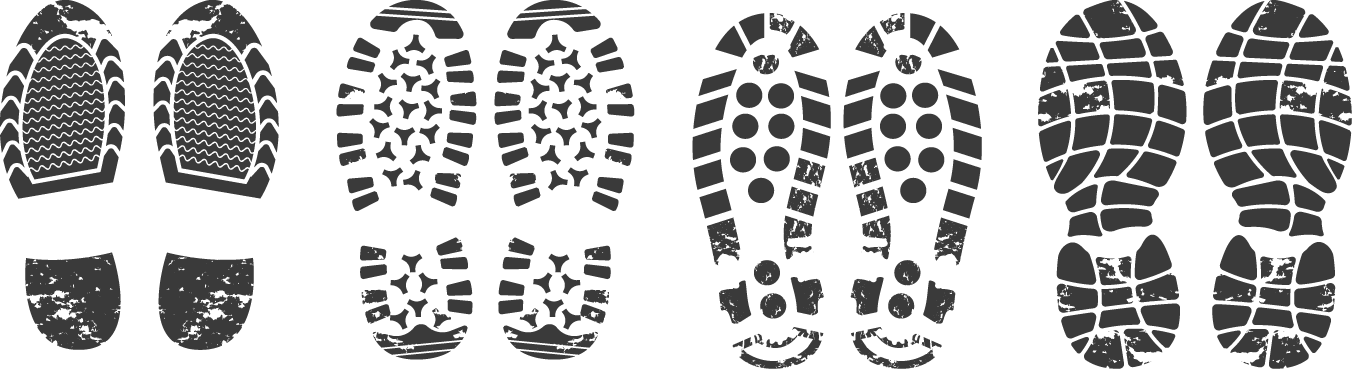
The shoe-making machine is an integrated equipment that combines mechanical, electrical, and hydraulic systems. Its performance is complex and requires high control precision. Typically, it is expected to produce different types and specifications of shoe bottoms while operating continuously. This particular dual-color shoe-making machine is specifically designed for producing shoe bottoms made from TPR and PVC materials. TPR shoe bottoms are a synthetic material composed of TPE and rubber, known for their diverse designs, excellent touch feel, vibrant colors, high glossiness, and advanced technology. Additionally, they are 100% recyclable, making them an environmentally friendly shoe material choice.
▸ It is desirable to have a concise and intuitive display interface, along with a convenient method for updating parameters. Currently, when changing shoe molds, it is necessary to manually modify the parameters of each workstation to accommodate different molds, making the parameter input process cumbersome. It is hoped that different mold parameters can be grouped into a preset mode for selection, allowing for the simple selection of the corresponding preset when needed.
▸ Due to the company's policies on equipment maintenance, there are requirements for regularly reporting on the operational status of the equipment. Therefore, it is necessary to provide corresponding equipment alarm information and support for exporting data to a PC. The ability to export historical data for analyzing alarm information and its causes is also crucial. Additionally, during the occurrence of an alarm, it is essential to promptly display the specific details.
▸ By placing different shoe molds on different workstations, various shoe bottom styles can be produced. However, when using different molds, the system parameters required will also vary, including factors such as the motor's advancement distance, cylinder's pressing time, and heating duration. Manually adjusting these parameters can be a tedious task.
Fortunately, the recipe function of the Yonghong touch screen solves this issue. With the recipe feature, there is no need to manually input parameter specifications. Instead, thousands of mold types can be imported at once, covering a wide range of mold requirements. This eliminates the need to manually load corresponding mold parameters for each different mold, greatly enhancing operational convenience.
Moreover, the system supports direct import of CSV files into the recipe table. Additionally, a recipe name search function is available, allowing for quick selection of recipes based on their names. These features significantly streamline the process and improve efficiency.
▸ To ensure the normal operation of the equipment, regular maintenance and servicing are essential. Among these, alarm information during operation periods is also crucial. Statistical analysis and summary of alarm data during equipment operation contribute to stability analysis and the formulation of preventive measures.
The alarm component in the Yonghong touch screen features a data export function. This allows for the export of past alarm records in CSV file format to a USB drive, facilitating the compilation and analysis of alarm data. Furthermore, in the event of abnormalities during the production process, such as material shortages, insufficient air pressure, or cylinder leaks leading to positional issues, specific warning messages will be displayed on the touch screen LCD monitor (e.g., "Material shortage at workstation 1, please check"). At this point, the on-site operator needs to confirm the situation and press the alarm clearance button.
Additionally, there are two alarm display modes: a running light alarm and an alarm display in list form. These provide a visual representation of the current alarm status of the equipment, enabling operators to quickly identify and respond to any issues.
▸ Through the data collection functionality of the SCADA software, it is possible to achieve a 24-hour uninterrupted data acquisition effect. Not only can the collected data be visually presented through historical trend charts, but it can also be periodically transmitted to other PCs on the local area network or saved to the current computer through FTP transmission. This enables system backup and the ability to view data history, ensuring the availability and integrity of critical information.
“One-click Instant Mold Parameter Switching”
This feature enables diversified shoe bottom production by eliminating the need to manually load corresponding mold parameters for different molds.
“Real-time Accurate Alarm System”
The alarm system provides two types of alarm display statuses: a running light alarm and an alarm display in list form. These displays visually indicate the current alarm status of the equipment, facilitating problem identification for customers. Additionally, alarm record data is stored for future reference.
“Quick Product Name Search”
In scenarios where there are numerous mold parameters, the system supports a recipe name search function to quickly find the corresponding mold recipe.
The fully automatic dual-color shoe bottom machine utilizes fixed mold, mold opening, and mold locking to enhance production speed, reduce labor intensity, and lower production costs. It boasts significant advantages such as high precision, high efficiency, convenient and safe operation. With vast market potential, it offers remarkable economic and social benefits.
Users can set, store, and download recipes based on different molds, eliminating the need for repeated parameter modifications. Additionally, the machine supports a recipe name search function, enabling quick retrieval of corresponding mold recipes in scenarios with numerous mold parameters.
In the event of any abnormalities during the operation of the equipment, detailed information is promptly displayed along with corresponding troubleshooting methods. This allows operators to quickly resolve issues and minimize any impact on production. The compilation of alarm data contributes to stability analysis and the formulation of preventive measures for equipment production.
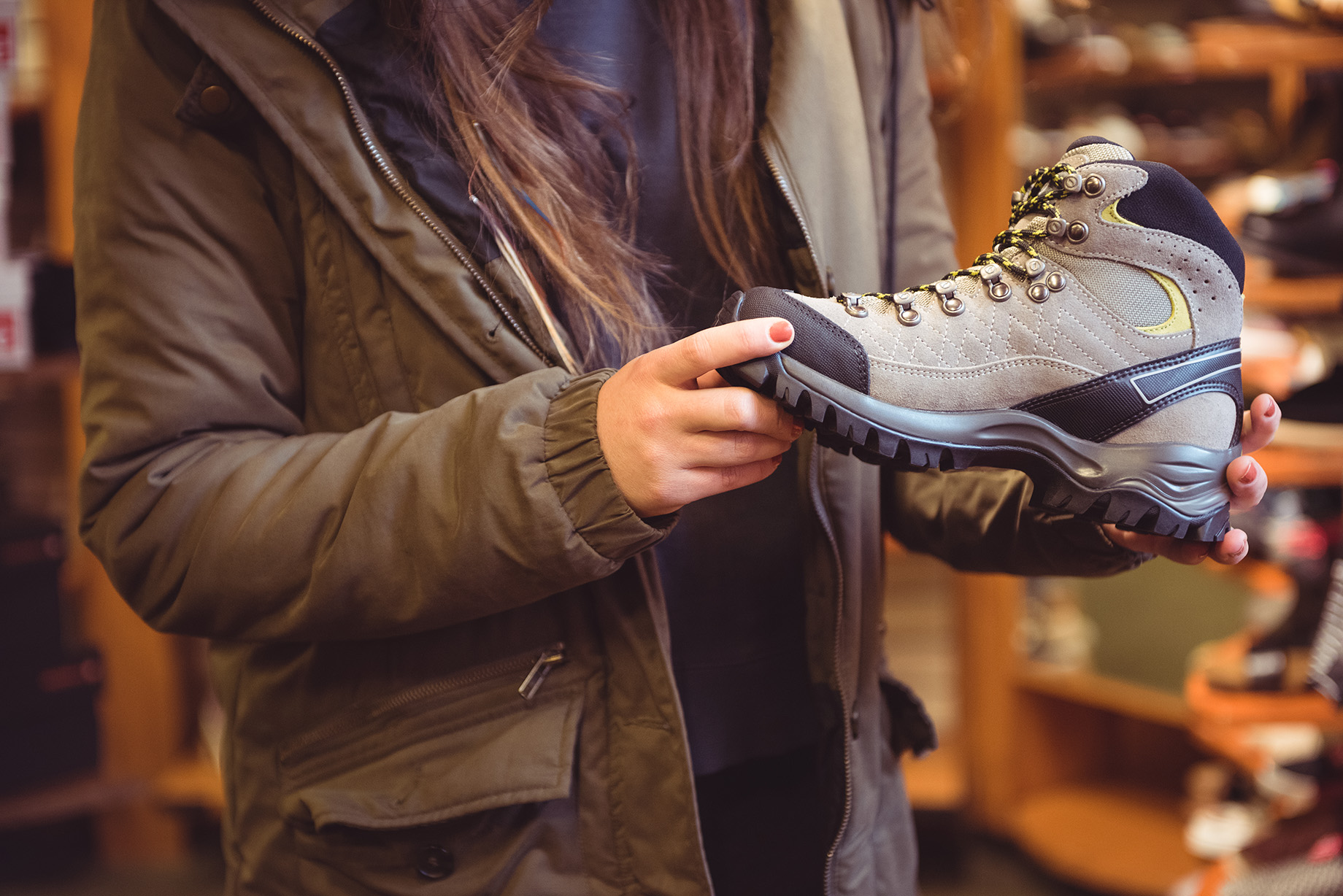